I have a question i cant seem to find an answer too, even on Garretts website. Im hoping one of you guys can explain this to me.
Suppose you size your turbo to be able to give you enough flow to have around 400HP. Suppose that means your turbo will be intaking 530 CFM's. What will be the flow rate in CFM's out of the turbo?
Heres what I see. If i go to garretts website, they walk you through step by step on how to size all of the components you would need for a tubo system. In the example, they show you how to size an air filter for 530CFM's of flow. So, we know that the turbo will be taking 500 CFMs from the atmoshere. Next, they show you how to size charge pipes, but again they use the same 530CFM's as the guiding metric. I just dont understand at this point...
To me, im thinking Cubic Feet Per MInute is a measurement of Physical VOLUME.... not a measurement of quantity of mass, like lbs/min would be. So, if you take in 530CFMs, and your turbo pressurizes it, shouldn't this VOLUME DECREASE? Im mean, dont you pressurize things by smashing them smaller! Shouldn't my 530CFM that came in at 100KPA now be 200KPA (if you went to 14.7 PSI with your boost pressure) but read a lesser CFM, such as 265 CFM's? becuase the act of pressurizing it made it fit into a smaller space. so, i cannot agree with Garretts website saying i should size my charge pipes to flow the same amount my turbo inlet does. it makes no sence. However, I do understand that each one of my CFM's packs a much denser oxygen content becuase it is under pressure, and more oxygen has been packed into each Cubic Foot as measured pyscially, and therefore wieght of each CFM is greater. again, those are the ways you can tell your moving more quantity of air even though it physically has the same dimentions.
another way of saying it, lets say you had a empty nitrous bottle. it would have 1 cubic foot of emtpy space. it would wieght lets say 10lbs. now, when you fill it, the bottle stays the same physical size, but pressure goes up dramatically, so therefore wieght does to, indicating product is going in, and it ends up wieghing 50lbs when its full. however, it is STILL THE SAME PHYSICAL size. 1 cubic foot is 1 cubic foot no matter what its pressure content or density is, becuase 1 cubic foot is a physical dimention measurement. likewise, if you took this bottle outside and inserted the bottle outlet into the worlds largest trashbag, and open the valve, what was once 1 cubic foot would depressurize and expand to become HUNDREDS of cubic feet. So, when things pressurize, the take up less space, and when they depressurize, they take up more space.
so, i do not see how you can take 530 CFMs, pressurise it to 14.7 PSI and still come out with 530 CFM.s This makes no sence to me, can someone please explain how garretts website can be right or wrong?
http://www.turbobygarrett.com/turbobygarrett/tech_center/turbo_optimization.html
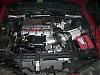
M90'd Built LGO-15 PSI
http://webstarts.com/quadper4mance
You're looking at it the wrong way.
**so, i do not see how you can take 530 CFMs, pressurise it to 14.7 PSI and still come out with 530 CFM.s***
CFM is a standard measurment used in all kinds of calcs...
Umm, how can I put this...
When they say CFM, it's how much volume that gas would occupy IF it was a XX temp and at XX presure. (You can convert it any way you want, but it all comes down to a standard.)
Did that answer your question ? Hard to explain.
11.92 @ 122.69 MPH Rotrex Blower / Intercooled / Water-Meth / 100% Daily Driver / 381 WHP
kinda complicated, but if you're bored :
http://en.wikipedia.org/wiki/Ideal_gas
Heh, i had to stay awake during my fluid dynamics classes, so no reason why you can't read that. lol.
11.92 @ 122.69 MPH Rotrex Blower / Intercooled / Water-Meth / 100% Daily Driver / 381 WHP
Righto. He's got the right idea, that the same amount of air now fits into a smaller volume, but as mentioned here, that's largely irrelevant to the engine's consumption, for the oxygen content is not altered. All the engine knows is how much oxygen is available to support fuel combustion, no matter what pressure it's delivered at.
CFM is a standard, measured at a standard atmospheric pressure. It can also be converted to HP rather easily. If any one wants that formula, let me know...I don't have it at hand right now, but I do have it at work.
Bill Hahn Jr.
Hahn RaceCraft

World's Quickest and Fastest Street J-Bodies
Turbocharging GM FWD's since 1988
www.turbosystem.com
Excellent! That is the missing link in my head... I did not know that Cubic Feet was at a standardized temperature and pressure. Thanks guys.
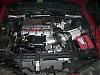
M90'd Built LGO-15 PSI
http://webstarts.com/quadper4mance
Alright guys, I just wanna say i really appreciate you sharing the above info with me, its really changed my entire approach to my car/tuning endeavors. However, I am now faced with another "theory" and i dont understand the "how", i only understand the "result".
lets stay with the same numbers as above. so, say you take in your normal 530 CFM's into your blower or turbo, and it pressurizes it to 14.7PSI. The outlet of the compressor air will now be 530 CFMs @ 14.7PSI and lets say 220*F. <-- just a stab at temp. doesnt matter for the question really.
okay, so with your 530 cfms, you can then figure out roughtly what HP level you can produce with that quantity of air molecules. So, i see the avg is .7.
So, 530 x .7 = 371HP at the crankshaft. sounds close enough, right?
okay, heres the question...
by adding a properly sized/flowing FMIC, what exactly is happening to the air charge? How is more HP being created?
Is is becuase the Temp drops cuases charge to contract, and put more CFMs into the same volume? In which case the CFM going into the motor is a larger number than what is actually being induced into the turbo inlet? This makes no sence to me, so i must ask you guys to explain for me.
I see that an properly sized IC should give you about a 20% power gain, so that would likewize suggest a 20% CFM gain would it not? If there is no CFM gain from what the turbo takes in versus what the engine takes in, where are the extra air molecules coming from?
I appreciate your responces, im really trying to learn this stuff on a deep level. thanks.
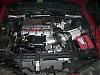
M90'd Built LGO-15 PSI
http://webstarts.com/quadper4mance
Intercoolers create additional power in two significant ways:
1. The decrease in temperature increases oxygen content per volume. More oxygen delivered to the engine = the ability to burn more fuel = more power.
2. The engine can run more advanced ignition timing with a cooler inlet temperature, thus make more power from additional timing advance without detonation.
There are some finer points too, but these are the home runs an intercooler can achieve!
Bill Hahn Jr.
Hahn RaceCraft

World's Quickest and Fastest Street J-Bodies
Turbocharging GM FWD's since 1988
www.turbosystem.com
won't the cooler air become more dense which means more power.
That would be item #1, yes. Density!
Bill Hahn Jr.
Hahn RaceCraft

World's Quickest and Fastest Street J-Bodies
Turbocharging GM FWD's since 1988
www.turbosystem.com
look at it from a pressure stand point... think of a balloon...or a tire... how much air (in cubic feet) is really crammed into a tire that has 40psi of pressure... think about when you fill up that empty tire... it starts off 0 psi... with standard unpressurized air which would take up just the geometric volume... now just think... you continue to fill up the tire more and more... now all of that air keeps going in yet the size of the tire stays the same(for the most part)... you are increasing the volume by compacting the molecules tighter and tighter together forcing more and more air in... and thats just like an engine... hence the name forced air... i hope that helped...
...I am the BEST at what I do...
"I guess your right[BlueBoost]. Me and my slow car are failers."
Blue, I get it.
Bill, I understand those are the RESULTS of using an IC, but i want to understand the HOW. I understand that lowering the charge temp raises the charge density. I understand that it is denser when colder, becuase more molecules are packed into an even tighter area. But, the part where i lose it is this... Lets say from BlueBoost's example above, if we were to fill that car tire full of air to a certain pressure above atmopheric,the tires physical size would grow and the tires temperature would also increase to a specific temperature based on Ideal Gas law. Now lets say by adding an intercooler to the tire, its internal air temp drops significantly... What happens to the tire? I say it must shrink in physical size due to contraction of the charge. Thats what would make sence to me. how bout you?
Now back to car engines. If the IC dropped temp of the charge, and therefore phsical size of the charge, then i would also reason that boost pressure would drop, becuase now the same charge is occupying less space. and if it occupies less space, but the container cannot shink to fit it (like a car tire could), the i would assume the pressure must go down, again, due to ideal gas law.
But alas! What we find in practice is there is only a very slight drop in pressure across an IC if properly sized, even when accompanied by a HUGE temp drop. So, the only way i can reason this could be true is if MORE CFM's were permitted to take up this now "extra" space to preserve boost pressure. If this is true, then it does in fact mean that becuase the Intercooler in doing its job, it is permitting more CFMs to enter the engine than what is being injested by the turbo/supercharger. And that i find equally strange/fascinating.
So, if you see something wrong with my thinking here, please explain, and you dont have to sugar coat it for me. Just tell me how it is in the most true context you can, even if it sounds like techno-talk. I can handle it.
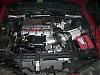
M90'd Built LGO-15 PSI
http://webstarts.com/quadper4mance
You can't add an intercooler to the tire...intercoolers only work when we have flow in and out, like an engine. It's impossible to intercool a reservoir of air such as a tire. So, put that analogy aside.
It's all about getting more oxygen into the engine. Air that is compressed (such as by a turbocharger or supercharger) also has heat added to it by the compressive forces As we squeeze the molecules closer together, there is friction released as heat). The air expands from the heat, taking up a larger volume, but wih the same amount of oxygen as prior to heating...now it's just taking up more space due to being heated (less air density).
When we then cool this heated air with our intercooler, it in essence "shrinks"...now we are packing more oxygen molecules into the same space. Since the engine is essentially an air pump, with a given amount of displacement intake per cycle, the more oxygen we can get into it, the more power we can make. Without the intercooler, the lower air density will mean less oxygen in the cylinders.
No, the engine is ingesting exactly the same amount of air as the turbocharger or supercharger is. It's just that with intercooling, we can increase boost pressure and ignition timing, and cause the turbo/super to ingest more air than without intercooling. Were we to run the same boost pressure and timing without intercooling, we'd experience detonation. So, without an intercooler, we have to turn down the boost and the timing to stay safe.
Bill Hahn Jr.
Hahn RaceCraft

World's Quickest and Fastest Street J-Bodies
Turbocharging GM FWD's since 1988
www.turbosystem.com
Bill Hahn Jr. wrote: You can't add an intercooler to the tire...intercoolers only work when we have flow in and out, like an engine. It's impossible to intercool a reservoir of air such as a tire. So, put that analogy aside. .
Agreed, you cannot add an IC to a tire, but it was funny wasnt it? lol However, you can cool the tire. and cooling the tire would cuase it to shrink in size. and it shrinks in size becuase it is physically capable of doing so. Unlike charge pipes and manifolds, which are ridid in there size, they cannot grow and contract to size match the charge within them. So, if the charge were to "shrink" due to cooling in a rigid system, then the pressure would have to drop as well. if its shrinks, its taking up less space. it its taking up less space, it has to have less pressure on a rigid containment system.
So, if the air would cool and cuase the tire to contract in a plyable system, please explain why it would behave differently in a rigid system and not shrink. becuase if it did shrink, it would have to lose pressure.
Bill Hahn Jr. wrote: It's all about getting more oxygen into the engine. Air that is compressed (such as by a turbocharger or supercharger) also has heat added to it by the compressive forces As we squeeze the molecules closer together, there is friction released as heat). The air expands from the heat, taking up a larger volume, but wih the same amount of oxygen as prior to heating...now it's just taking up more space due to being heated (less air density)..
Here you are acknowledging that by adding heat you expand the charge, and thus reduce its density. you even say becuase its hot, it takes up more space. Why would you say the inverse is not true... that cooling the charge would cause it to take up less space? If you were to simply heat up a gas in a static containment system, its pressure would rise, becuase it is taking up more space. agreed? so if you cool it then it must take up less space, and therefore lose pressure. has too, but you dont seem to agree with that statement.
Bill Hahn Jr. wrote: When we then cool this heated air with our intercooler, it in essence "shrinks"...now we are packing more oxygen molecules into the same space..
Here you say it again, it shrinks. we pack more oxygen in to the same space. dont you see how it would be impossible to maintain pressure without the addition of more air to take up the space the newly cooled charge retracted from?
.
Bill Hahn Jr. wrote: Without the intercooler, the lower air density will mean less oxygen in the cylinders...
Seems like you agree, with less CFMs taking up the same space becuase its hotter, then you would get less air into the cylendars than if you were to cool it down, contract the charge, but make more room for a few extra CFM's to squeeze in and take up the extra space, which would maintain the pressure. It seems we are both saying the same thing, maybe you just havent thought it thru to this extent before becuase you follow up with this....
Bill Hahn Jr. wrote: No, the engine is ingesting exactly the same amount of air as the turbocharger or supercharger is.
..
I dont see how this would be possible knowing that the charge contracted, but pressure remained steady. the only way for that to happen would be if more cfms were exiting the IC than entering it. and if that is true, then the motor is definately intaking more CFM's than the TC/SC is.
Bill, I appreciate you responces, and please dont be offended by my replys. I still havent seen a reason for the temp drop and pressure constant other than my theory. Im not sure if i was asking my question well enough to get that point across or not. So, Im not really argueing with your replys, or even saying your wrong, Im just pointing out my question more, thats all. my question doesnt have anything to do with timing advance, or upping the boost, or detonation. I understand all that stuff, but its not what my core question is about.
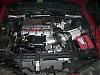
M90'd Built LGO-15 PSI
http://webstarts.com/quadper4mance
I won't take the above point by point...I'd prefer to just answer what appears to be your underlying question:
Boost Pressure remains constant because the turbocharger or supercharger will typically be called upon to pressurize more air to account for the loss of pressure due to density increase caused by the intercooler. In supercharged systems in particular, intercooling is always accompanied by a minor manifold boost pressure drop for this reason. To return to non-intercooled boost levels, a pulley change will be required.
In Turbocharged systems, the same will be seen, but since the turbocharger is a variable output device as compared to the supercharger, in many cases it just increases its own output to compensate (depending on where the wastegate actuator pressure source is, either upstream or downstream of intercooler).
Your problem in being able to visualize these factors may be that you perceive the gain in density would be accompanied by a plummet in boost pressure. This is not the case; it's a much less pronounced effect.
As an aside: Since most intercooled systems are built from the ground up to achieve certain boost pressure, the method is simply to adjust boost as needed to hit the target, not having to take into account these subtleties.
Hope this helps you "get it"; I'm not sure I can explain it in any more detail!
Bill Hahn Jr.
Hahn RaceCraft

World's Quickest and Fastest Street J-Bodies
Turbocharging GM FWD's since 1988
www.turbosystem.com
I don't mean to thread jack, but reading your response Bill, it raised a question for me. Where would be the better spot for a WG pressure signal, Pre-intercooler or Post-intercooler? I'd assume Post-intercooler seeing as there'd be a more accurate reading of what the engine is actually ingesting. Is that correct?
It's a good question! Invariably, OEM installations use the compressor housing. I believe this to be their choice for best wastegate response to rapidly rising boost pressure...especially in intercooled systems, there is a small but involved signal delay due to the distance, pressure drop, and volume between comp. hsng and the actual intake manifold. So, the comp housing is the best place if your boost "spikes" when wastegate is sourced at manifold.
So, where's the "best" place? It varies with the combo. If no undesirable spike is evident, sourcing wastegate at intake manifold is fine.
Also...as compared to sourcing wastegate at compressor housing, sourcing it at the intake manifold will typically raise boost pressure a PSI or two. This is due to the pressure drop across the intercooler and intake manifold. So, an easy way to vary one's boost up or down can be to change the source. Just be careful of Mr. Spike if you change it to the intake manifold.
Bill Hahn Jr.
Hahn RaceCraft

World's Quickest and Fastest Street J-Bodies
Turbocharging GM FWD's since 1988
www.turbosystem.com
If you're satsified with Bill's answer, stop here. He's right. This explanation uses math for people who like that kind of stuff.
Quote:
Suppose you size your turbo to be able to give you enough flow to have around 400HP. Suppose that means your turbo will be intaking 530 CFM's. What will be the flow rate in CFM's out of the turbo?
Just tell me how it is in the most true context you can, even if it sounds like techno-talk. I can handle it.
It depends on the compressor's efficiency. You can convert the mass flow to volumetric flow with the temperature of air at the compressor outlet using the Ideal Gas Law:
V(cu.ft./min) = n(lbs/min) x 10.73 x T(deg R)
(29 x P(psia))
V = Volume flow
n = mass flow
T = temp in deg Rankine (deg F plus 460)
P = pressure
A compressor's efficiency is defined by how much it heats vs how much it compresses. Using the map for the compressor you like, select the lines for pressure ratio and mass flow required to generate the power you expect and determine the compressor efficiency at the intersecting point. If we use Garrett's calculated boost pressure of 26.4 psi for 400 hp from a 2.0 l engine, and the flow map which Garrett calls "acceptable:"
We notice efficiency is around 75% at the point where mass flow intercepts pressure ratio.
We can rearrange the compressor efficiency formula to determine temp.
Tout = Tin + Tin x [-1+(Pout/Pin)^0.263]
efficiency
Tout = outlet temp deg R
Tin = inlet temp deg R
Pout = absolute outlet pressure
Pin = absolute inlet pressure
We can say the compressor map is based on inlet air at standard atmospheric temp and pressure. Probably not exactly right, but close enough. So Tin is 59 deg F. Pout is already calculated as shown on Garrett's pages (I'm using 41.1 psi). Pin is based on your altitude, I'm using sea level at 14.7 psi.
Tout = 519 + 519 * [ -1+(41.1/14.7)^.263]
.75
= 733.86 deg R
Plugging back into the ideal gas law,
V(cu.ft./min) = n(lbs/min) x 10.73 x T(deg R)
(29 x P(psia))
We get
V = 44 lbs/min * 10.73 * 733.86
(29*26.4)
= 452.547 CFM
So, where flow in = 530 cfm, flow out = 452.547 cfm. Volume flow is lost, as suspected, due to compression. Problem for you, trying to "imagine" what happens. Imagination is amazing thing and helps creativity, but not so good as a predictor based on physics. Follow the math and you'll find your answers.
Quote:
If the IC dropped temp of the charge, and therefore phsical size of the charge, then i would also reason that boost pressure would drop, becuase now the same charge is occupying less space.
First, change your head. Charge occupies same space. From vacuum to thousands of psi pressure, this charge occupies same volume and is same "physical size." Think of molecules of air bouncing off each other. Adding heat energy makes them move faster, bounce harder. So does putting more of them into your "container" provided heat energy isn't removed at the same time. Pressure is measure of "bounciness."
Quote:
What we find in practice is there is only a very slight drop in pressure across an IC if properly sized, even when accompanied by a HUGE temp drop. So, the only way i can reason this could be true is if MORE CFM's were permitted to take up this now "extra" space to preserve boost pressure.
Cooling the charge between compressor outlet and TB does cause pressure drop across the cooler, but only in relation to the restriction provided by the cooler. You can only measure pressure caused by flow when you have points of restriction. If you cool the charge across the intake tract with a cooler and tract that provides no restriction then pressure drop measured with a boost gauge would seem relatively constant from turbo outlet to TB. So technically, when the ad or article says "with a big cooler we see no pressure drop from inlet to outlet" you can believe 1) it's close to the truth, and 2) the compressor outlet pressure will measure lower as a result.
Quote:
If this is true, then it does in fact mean that becuase the Intercooler in doing its job, it is permitting more CFMs to enter the engine than what is being injested by the turbo/supercharger. And that i find equally strange/fascinating.
This is thinking in volume again. Stop it! Volume flow is related to mass flow through density. Anything which affects density affects volume flow. It's a math thing. Compressor and intercooler are biggest players in changing density but not only ones. Also, volume flow through compressor cannot be greater at outlet than inlet, else your "compressor" is actually an "expander." Or in turbo lingo, when volume flow increases across the wheel, the device your looking at is the turbine.
Now... why is a lower charge temp associated with higher power levels? Imagine two scenarios. In the first, you have two systems with equal pressure but unequal temperatures. The system with the lower temperature will be delivering greater mass flow and therefore more O2 to react with fuel. In the second case, you have two systems delivering the same mass air. One is at a lower temp and higher density. The lower temp air is more likely to resist detonation which may allow ignition timing which is optimum for maximum power. The reality is a combination of these two examples. Post intercooler air is denser, and it's also less detonation friendly.
hth
-->Slow
I am stuck thinking in volume becuase the basis of this entire question is so i can properly size my pressure pipes and intercooler. To determine what size pipe is required for me to transfer my charge from point a to point b is going to be based on volume, not density. and agian, when sizing my FMIC, its physical dimentions are based soley on volume flow, not charge density. So, this is why im not really interested in hearing about what the motor does with the air it recieves... that information will not help me size my transfer system.
the reason i am baffled is becuase i have 2.5" charge piping thru my entire system, and am moving 630 cfms thru the intake of my charger, yet i cannot efficiently get this volume to my intake manifold. I am trying to figure out why. I am dropping 4psi accross my FMIC that measures 3x12x32, and another 3 PSI across my piping. This is my third IC and it will not flow what i need. #1, I cannot find ANYONE ANYWHERE to tell me how to size a FMIC to make sure it will flow a particular CFM volume. But, with this one i have now, i find that it begins restricting at 480CFMs. at this point, my engine is only at 4400 RPMs, so, once this happens, as my engine RPMs increase, my SC just builds more boost on the hot side of the IC, yet i get no more flow out of the cold side. the real problem with this is, a roots blower is not for making excessive boost. i have measured upto 18PSI inside my blower casing under these circumstances. This is cuasing the blower to draw crazy amounts of power off the crank, all for nothing, becuase no matter how hard it works, only 480 CFMs are getting thru. So, i removed the IC and straightpiped the connection, and i actually gain alot of WHP! But then the air is almost 280*F, so thats no good. I recently contacted Bell Intercooler about what size FMIC would flow 630... the salesman told me to get size 4.5 x 12 x 28... but he simply refused to give me the formula he was using to figure that out. He said it only applies to his IC's and it would be useless to use to compair to anything else. I know where he's coming from, he dont want to give me info i need and then i go somewhere else and buy one cheaper. his IC was 1150.00 assembled and shipped!!!! I thought that was kind of a dueche bag though, he refused to educate his potential customer. that made me feel like he was saying.." just give me your money, shut up and trust me" He may be right, but im not chucking 1200 bux on a f'n IC on the basis of trust. Ive already bought 3 IC's that people claimed flowed 600CFMs, and i trusted them, but got burned every time. so why should i trust guy #4??? I WANT TO SEE THE MATH!
So, how can i determine what size piping i need?
How can i determine what physical size FMIC i need?
Why do i see alot of people using a larger pipe after the IC than before the IC? This suggests more CFMs are being transfered after the FMIC. But again, nobody really seems to know anything, and those that do post it far and few between, so its hard to find. So i do appreciate the responces so far.
Slowolej- thanks, i will read this a couple times and make sure it goes into my head. I do appreciate you taking the time to write that up for me.
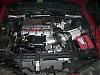
M90'd Built LGO-15 PSI
http://webstarts.com/quadper4mance
Nukkinfuttz wrote:I am stuck thinking in volume becuase the basis of this entire question is so i can properly size my pressure pipes and intercooler. To determine what size pipe is required for me to transfer my charge from point a to point b is going to be based on volume, not density. and agian, when sizing my FMIC, its physical dimentions are based soley on volume flow, not charge density. So, this is why im not really interested in hearing about what the motor does with the air it recieves... that information will not help me size my transfer system.
I really have very little to interject on the subject as I think Bill and Slow covered the subject quite well without actual teaching a full lesson on thermodynamics.
Now I'm not sure on this one but aren't CFM's actually the cubic feet per minute of the gas that would be flowing at standard temperature and pressure? So CFM's (or volumetric flow) is not dependent on actual volume at all...it's simply a way to (more) easily translate a set amount of volumetric flow into actual mass? I'm pretty sure I remember it being explained to me at some point in time this way, plus everything would then make a whole lot more sense because while the flow IS boost dependent, you can now simply look it up on the compressor map and convert to volume without accounting for boost in your calculations.
Please correct me if I'm wrong on this one. All of the questions in this thread are all ones I've been a bit fuzzy on for quite some time so thanks guys!
Seems like a hundred questions piled in here. Where to start? Lessee...
Original question boils down to "Can turbocharger change flow to accommodate density changes?" Answer: Since the turbocharger is powered by exhaust heat and compressor output is regulated based on pressure, the system is somewhat self correcting when density changes are introduced. This is especially true if the pressure signal is referenced to the intake manifold."
Now: I believe the problem you're trying to solve is not the problem you need to solve.
You really need to accept the relationship between mass flow, volume flow, and density. When mass flow is constant and density increases, volume flow decreases. This is even more important for you than a turbo guy. If you add an intercooler to a system running a given mass flow (i.e. supercharger) you will increase air density at the cooler outlet and reduce volume flow. What you're asking for is a way to keep volume flow constant when density changes. That would mean adding mass flow, something a cooler is not able to do.
You cannot get anyone to give you a way to calculate ic sizing for a specific volume flow is because volume flow is related to mass flow through density, and density change across the cooler is dependent on outside variables. You could calculate density change across a cooler using cooler efficiency then use that number and volume flow before the cooler to calculate change in volume flow, but you'll have to specify variables like outside temperature and inlet temperature, something the ic salesmen can't do.
Now you say there's a restriction at 480 cfm. My first question is how are you measuring this? Taking the number for granted, I notice on the M90 map that stock compressor flow at the inlet is at 480cfm around 10000 to 11000 rpm. If you're measuring flow at the outlet then compressor speed is even higher. I have to wonder if compressor efficiency is going to hell here. Your volume flow is maxed out, yet the air pressure and temperature is increasing meaning air density is decreasing. Looks like the compressor just can't do the job you're asking it to do. But your cooler is able to do a good job of reducing air temp and increasing air density. Too bad your engine doesn't see enough pressure at that point to take advantage of it.
Now here's something to think about...
Quote:
But then the air is almost 280*F, so thats no good.
Really? Are you sure? You made more power, true? Did you have problems with detonation? Overheating? Preignition? Is this an issue of "everyone says..."? Look at the factory mounting point for the 86-87 Buick GN intercooler. Interheater is more like it, mounted after the radiator. And how about the power squeezed from the non-intercooled "hot air" versions? Pretty good considering the turbo outlet temps were at least as high as what you're seeing. I ran through some density calculations once and came up with a basic relationship which I still use today. A 50 deg drop in air temp is worth a 1 psi increase in boost pressure. At this point I'd probably opt for a smaller cooler and let the remaining pressure have fun.
As far as calculating tubing sizes, Garrett gives a guideline for a good bend radius so bends won't be too restrictive. Pre-cooler pipe diameter can be calculated based on compressor volume flow at the outlet and post cooler pipe size can be calculated after determine change in flow through the cooler based on density change. Pipe should be smaller post cooler to maintain pressure. Not sure why larger pipes are used.
-->Slow
Found better / newer / different compressor map. Still interested in hearing how airflow measurements are taken along with pre-cooler pressure and compressor speed and / or pulley ratio.
-->Slow
That is correct, I based my CFM restriciton point of 480 CFMs on the M90 compressor map. let me explain.
I datalog a WOT run. Then i notice my WHP begins to level and then actually fall right at 5400 RPMs on the engine. So, I am using a LD9 crank pulley that is 6.5" OD and a 3.4" OD SC pulley, yeilding a Pulley ratio of 1.911. I take this and multiply it by 5400 RPMs, and get 10323 RPMs on the blower. I take that info and look at the compressor map, and see that is around 480'ish.
I have also added 1/8" NPT-to-Barb fittings in my blower case, and in both my IC end tanks. I can see that at 5400 RPMs, i begin building a crapload of boost in the blower casing and hot side end tank (over 18PSI) , but nothing changes in the cold side end tank. This is cuasing the BSFC of the motor go rise exponentially, becuase the SC is stealling all the available power off the crankshaft to drive itself. I can even set in neutral, and push my pedal to the floor WOT, and get this, RPMS will go to 6800 RPMs, and then the motor will not accelerate any more! It even starts making full boost, 10 PSI in the manifold, no load, and a solid 6800 RPMs. Thats how much power the SC is taking off the crankshaft! alot! So, i have got to get this transfer system sized right.
What i am doing in the mean time is switching back to a HO pulley that is 5.5" OD, which yeilds a pulley ratio of 1.617. This would make my top engine speed of 7200 RPMs to drive the blower to 11647RPMs. If you again refer to the compressor map, you will see that is about 500 CFMs'. This is ALOT closer to my flow restiction than the other pulley that was trying to send 630 CFMs thru this same system! So, im sure i will pick up lots of WHP becuase BSFC is gonna drop like a rock.
but, i would like to switch back to the higher flow settng if i could just figure out these things.
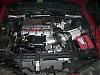
M90'd Built LGO-15 PSI
http://webstarts.com/quadper4mance
Okay, i got my conversion back to the HO pulley done, and test drove the car. As predicted, my BSFC began to spike at exacltly 6798 Engine RPMs, so with the pulley ratio of 1.617 would be 10996RPMs on the SC'r. Again, looking at the M90 flow map, you see this is 480 CFMs'. So, that double confirms the problem is flow restriction, becuase i can move the problem around in a predictable manner with pulley changes.
and of course, i have picked up a crapload of WHP becuase i now have less BSFC due to SC drive loss. Whoever thought a slower pulley would make you go faster? lol
so, what should my next move be?
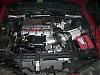
M90'd Built LGO-15 PSI
http://webstarts.com/quadper4mance
Quote:
So, that double confirms the problem is flow restriction, becuase i can move the problem around in a predictable manner with pulley changes.
There's really no way to determine what cooler you'll need without relying on a manufacturer. Cooler size is only part of the picture. Internal construction, restrictions, &etc all affect the selection process. I'm sure you've read this, but without any manufacturer data, there's no way to factor in these variables in a simple calculation. You could discuss efficiency and pressure drop and try to calculate backward but you're still at the salesman's mercy if he lies about the efficiency.
I was thinking about running two coolers in parallel and what a hassle that would be to attach to the car, and something dawned on me. Why not use a compressor relief valve and bypass tube to bypass some air around the cooler? Set it for about 8-9 psi and it will allow pressurized air to scoot around the cooler when flow restriction begins to build. You'll still get some cooling at lower rpm which can help to reduce intake tract heating and you won't have to ditch the current cooler right away. Plus it's cheaper than a new cooler and it will confirm that the compressor is not getting out of it's efficiency range and has no chance of ever doing what you want.
FWIW, I'm sure you have a lot invested in the M90 and it's a cool thing to do, but looking at the compressor maps I'm just floored that peak efficiency is only 62%. The area you're trying to run the compressor in is slightly above 50%. There are better belt driven compressors out there.
-->Slow