hi guys..i was looking into starting my interior fibgerglassing project and figured id start with my door panels..cus who needs them to drive the car anyway right?..figured id get some practice with them...now when i took these things off i noticed they bend veryyyy easy...like just simply leaning on them makes them bend severly...howw can i keep this from totally breaking the fiberglass apart?or do i need to just glass and glass and glass till they are so solid you cant move them??
didnt know those things would sand smooth?? sounds like a good idea..if they didnt have cracks in them

...and yes i just want them nice and smooth..after that its on to the dash and console....but one thing at a time
Well not to take the post away.. but im look to start learn how to fiberglass... and i have a good idea of how.. but i want to total redo the way the panel looks ( layout ) any steps on how .... that cloth that you put the harder on ( couldnt spell the word ) and then bondo etc or where would i start
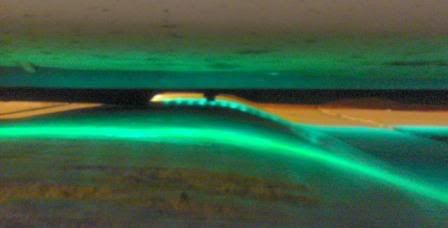
Change is Currently in effect!!!
sorry for not knowing the right terms help would be great tho
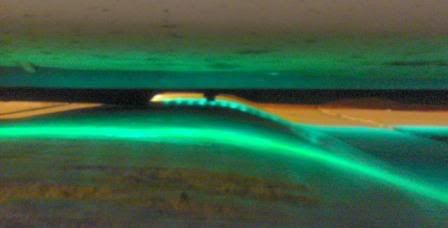
Change is Currently in effect!!!
use fleece for stretching your material. even foam works pretty good too, you can sand and shape out your design alot better (that is how I made my dash board) I actually used foam, sanded and cut it to the desired shape and fiberglassed over that. Once hard, I turned it upside down and ripped out the foam to leave me with a shell.
as for this post: are you changing the design/style? if not, just sand it smooth (it has the same finish as fiberglass)
ill try that with my center console thanks

...but my door panels have cracks..so i guess im just gonna have to get new ones before i start on them...so i guess ill just use these for practice
heres info on how to make kickpods, same steps can be used to make just about any fiberglass piece u want.
MATERIALS
Most any auto parts store should have fiberglass resin and cloth. You could also check your local boat shop. Most resins come with the proper hardening agent but make sure. You can buy extra hardener if u feel the need. Other things to pick up are 3” masking tape. Some towels some paper a half dozen cheap 1” brushes(the cheaper the better because the fiberglass will ruin them, u can usually find them for like 98 cents a piece) and a box of plastic gloves.(hardware stores have the thin kind almost like hospital gloves with like a pack of 10 for few dollars.)Also pick up a ¼” dowel rod a foot or so long, material to cover your kick panel pod like vinyl or carpet, or paint and a metal radio back strap,. Most audio stores have them laying around and will give u a couple for free if they have them. wood glue or a glue gun Bondo, a few long metal screws to screw your pods to the floor, and the most important item is a mask. You should be able to find them next to the fiberglass products. Check the back to make sure it’s good for fiberglassing. Fiberglass is very toxic stuff. Not only when you’re spreading it out. But 10x worse when you are sanding the fiberglass. Fiberglass dust particles if inhaled can do major damage to your lungs so make sure you spend the money on this.
INSTRUCTIONS
One thing I suggest is to do any sound damping and wiring before you begin your kicks. Once u put a layer or two or three of damping, and pull the carpet for that and running your wiring the carpet will fit back in a little different so it’s best to take care of that first. The way I started was to take a look under my carpet and see what’s behind it. Sometimes u will have wiring or a computer or such behind the carpet. This may need to be moved. Also while the carpet was pulled back I checked for an area where I could run a screw to mount the speaker pod. Now take your 3” wide masking tape and start taping off the area that you plan on making your kicks at. Lay the tape out with overlapping layers and tape off 3x the size of the area you want. Once u are twice the size of the area you need, you can take the paper and use it to cover the rest of the area further away. Reason being is fiberglass is nasty stuff. I didn’t quite make my tape area big enough and I got a drop of resin on my carpet, and that stuff doesn’t come out period. Make sure you have it all covered up. After I got a layer down I put another layer overtop of it where my kicks would be built just in case. It’s better to spend an extra 10 minutes covering up everything than to have a spill on an uncovered area and be stuck with a crusty carpet or door panel. Now some people use aluminum foil to lay out there area. But I like the tape because it stays down and u do not have to worry about moving it. Another nice feature about the tape is it will stick to your fiberglass mold. Which some don’t like but I do because when I’m test fitting the mold the tape is still there and the stickiness helps hold the panel in place during testing. Once the tape is in place it’s time to get started. For the first layer I just tend to do a layer of resin. When mixing the resin read the instructions. I like a plastic whip cream bowl its nice because the resin doesn’t stick, when it hardens you just flex and twist the bowl some and the resin pops out in a neat little mold of the bowl. They way I mixed was to basically just fill the bottom of the whip cream bowl and then count out around 15 drops of hardener. Then checked to see how long it took to dry. 15 minutes is about right. And then if it took longer I’d add a couple drops of hardener to the next batch and keep my count. After a couple of batches I had it down to where I just new how many drops I needed. It’s best when you’re just learning to work in small batches. I made the mistake of making a big batch and used way too much hardener, after 2 minutes it was hard as a rock and I had wasted a ¼ of the can. Once you learn the proper hardener to mix u can start using more resin. So once the first batch was mixed up I just took a brush and painted on a coat or resin. Be sure to wear gloves. I also made the mistake of not wearing them the first batch and I got a drop of resin on my hands so I thought, no big deal just go wash my hands, well that one drop smears when u try and clean it and I spend around 20 minutes trying to get the crud off my hands. Wear the gloves. Now after around 15 minutes the first batch had dried so for the second batch I started using the cloth sheets. Now the easiest way for me to do this as a beginner was to cut the cloth down to manageable sizes I used around a 6”x4” piece of cloth. As u progress you can leave the cloth bigger. I’d use the brush and wet down the panel, then lay down my cloth piece then brush on more resin, making sure the cloth stayed flat and that I got all the air bubbles out. This is important air bubbles trapped weakens the fiberglass. Think of a phone book when all the pages are flat it’s nearly impossible to rip in half. But if that same book was raised up and u could tear each individual page, every one of us could do it. So u need to make sure no air bubbles keeping the layers separated. Make sure the cloth is fully soaked with resin but don’t overdo it. Once you have a layer of cloth I like to alternate a layer of resin then a layer of cloth. Or u can do all layers of cloth. I did around 10 layers which makes a pretty strong backing. U can probably get by with 5 or 6 layers. But I tend to go overboard a bit. Once u have your backside built up. The next step is to make your baffle board. The baffle board is basically any board that will hold your speaker. Use medium density fiberboard (mdf) if you’re going to have serious midbass, I’d use ¾” mdf. But if it’s just for midrange and up you can get by with reinforce ¼” mdf. I like to use the reinforced ¼” mdf basically your just throwing a couple of layers of fiberglass on top when you’re finishing them up. This way the kicks are lighter yet just as strong. I always try to keep them as small as possible which the ¼” helps. Take a look at your kick panel area and try to get an idea of how u want the kicks pods to look. A popular design is the teardrop method with the tweeter an inch or two above the mid. It’s an easy design to work with as well. As a side note sometimes it is necessary to have the midrange and tweeter at slightly different angles so it might not be a bad idea to separate your baffle board so each piece can be angled. Once your mdf baffle board is cut to the desire shape with your holes cut for the speakers take the radio back strap and attach it with a screw to the backside of your baffle board and attach the other side to the middle portion of your fiberglass back. If your baffle board is big u may need to use two back strap pieces to hold the baffle in place. The reason for this is for testing and tuning and to achieve the proper angle.
IMAGING & STAGING
This is the most critical stage of the process. This is the whole point of building your own kicks for superior imaging and staging. Let me explain a little about why kick panel speaker pods work so well. Basically the goal you should be trying to achieve is a realistic soundstage. When you’re sitting in a car with proper speaker placement u can pick a nice selection, sit in the drivers seat close your eyes and have the sound be so accurate that u can point out where each musician is on the stage in front of you. To do this you need a good left to right speaker placement. When placed right the vocalist will be dead center of the dash. With the other musicians spread about the stage. Now the problem is path length differences. When the music from one speaker is reaching your ear way before the other speaker this will kill the staging and imaging of the sound. The goal is to get the left speaker the exact same distance from your ear as the right speaker. Now if your speakers are mounted on the dash the left speaker is say around 38” from your ears. And the right speaker is around 50” from your ears. Now if u lower the speakers into the doors the left speakers is 36” and the right speakers is 52” the difference is not as great so the times arrive more closely now drop them down in the kicks and the difference is 52 to the left speaker and 57 to the right now the distances are even closer. The further back in the kick u get the more equal your lengths will be. Some people think that because it’s low in the dash that it will sound like it’s on the floor. But with proper aiming it will sound like it eye level. The reason being your ears hear better left to right then they do up to down so it’s easier to fool your ears into an image having height then it is to fool the left and right separation. So now back to the instructions. With your baffle board mounted to the back of your kick pod with the metal back strap go ahead and mount your speakers in and wire them up. Then take a few towels and place them around your kick to absorb some of the sound. Then use a cd that is of high quality and that u know the setup. A really good disc is the iasca competition cd. It has layouts for each song showing you where each instrument should be placed which is really nice if you’re not that familiar with the music. It’s hard to tell if one of your favorite songs is imaging right if you don’t know where the musicians are supposed to be. Its just guessing in that instance and that won’t help you at all. Generally the vocalist will be in the center of the stage but that’s not always true either. So try and pick up a tuning cd that has a layout of where the instruments are. Use your source material and start listening. If u have a good home system that images well u can go back and forth between it and your car listening. Now just take your time and work with angling the baffle boards to adjust the sound to get it where you like it. Remember that after around 10 minutes your ears will become fatigues so take some breaks then go at it again. This is the most important part so take your time. I know several competitors that have spent over 40 hours just listening and aiming. To some that’s absurd, but I know they win a lot. I spent around 6 hours listening and adjusting in my grand am.
CONSTRUCTION
Now once you have the sweet spot found. Take the dowel rod and carefully cut some short pieces. What I did was cut some pieces of dowel rod to go behind the baffle board and attach to the fiberglass back. And glued them in. this helps keep the piece more solid. Then I looked at the kick and with a marker made an outline on the back kick panel piece where I wanted to cut it out. Once I had the outline done and each kick secure, I pulled out the speakers and removed the kick pod from the car. I double checked to make sure the kick pod was secure and wasn’t moving and I took my dremel and cut along my markers line to form the back. Now we have a back and front and the only thing were missing are the sides. Now there are several ways to go from here one way. The most popular way is to take your cloth, some will use sweatshirt material and stretch the material over the top of your baffle and around to the backside of your fiberglass backing. And glue it in place. Then mix a batch of resin and soak the material. Now this works well if the material can be stretched the way you want it to. On items that I need a special shape I’ll take expanding foam and spray it around the area I want, in my case I just filled in around the kick between the front and the back. Then I left it dry. Once it has completely dry I took a razor and shaped the foam to the desired shape, once I had the shape I wanted I just mixed up the resin and added a few layers to the foam. Making sure to get it around the edges from front to back so it was one entire piece, this way works great for goofy shapes that you just can’t get by stretching the cloth over. Now I applied around 4-5 layers of resin 2 of those layers included cloth like we did on the back. Once it was thoroughly hardened I just pulled the foam out through the speaker holes and I was ready to roll. Now the fun begins, sanding. Make sure you wear your mask, and I took my sander and sanded down the big pieces of resin that were misshapen, then I got out the bondo and basically smoothed the shape out. Bondo is basically like fiberglass resin but its more like putty, you mix it the same way and can use a putty knife to put it on. Once it hardens start sanding it down more and more to get it as smooth as possible. If you’re covering the kick panels in carpet it won’t have to be super smooth but if you plan on painting it or covering it in vinyl any dips or lumps or unsmooth areas with show through. So get it smooth as possible. Once its sanded smooth you can drill some small holes in the back for your wires cover the kick in your preferred material. And they are basically done. I used a single 2” metal screw to screw my kicks in. since the kick pods are molded to the contours of the floor they were sturdy and unable to move once screwed in. where you screw yours down at will vary depending on the car and on the size of the kick panel. You may have a design that requires 2 or 3 screws. Now this is basic instructions for a plain kick panel design, if you want to have the speaker recessed you’ll have to add a piece on top of your baffle to flush mount the speaker, different speakers have different mounting plates so you’ll have to check your speakers mounting requirements to see what’s necessary to recess the speaker.
I hope this helps you in your design of the kick panels. Once you get started try your own designs and ways to maybe improve on these instructions, and if you find a new way of doing it let me know.
http://www.flickr.com/photos/sndsgood/ https://www.facebook.com/#!/Square1Photography