http://www.aeroforcetech.com/ +
http://www.hptuners.com
can you have a obd2 port splitter so that both of these can work simultaneously?
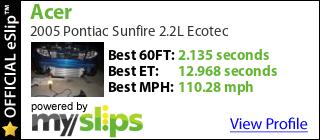
|Forged 8.9:1 Wiseco Pistons|Forged Eagle Rods|HPTuners|60trim|Tial Wastegate|
|Precision Intercooler|2.5" Exhaust|2.5" Charge Pipes|630CC Mototron Injectors|
|Stock: Fuel Pump, Transmission, Manifold, TB, Head, Head Gasket, Ignition, Suspension...|
No... I don't believe there is such a thing as an "obd port splitter"
This is why:
The scan tool has a specific "address" when it is connected into the bus. This address is hard coded in (I think its 0x10). That means the ECU will recieve requests from, and address responses to address 0x10. If two tools are on address 10, its not going to know which tool you mean for which response. HPT uses a special GM mode for transmitting large amounts of data very quickly, and if the other tool can't understand whats coming through the line, then its going to get confused. Not to mention that the data meant for the HPT cable will also get sent to the other cable, and confusing it by sending responses that it never requested.
4cyltuner.com - Information Source For 4 Cylinder Tuners
Buy stuff from CarCustoms Ebay! Won't be disappointed!
Aeroforce can do it, its possible to run a dual interceptor setup on the cobalts

1989 Turbo Trans Am #82, 2007 Cobalt SS G85
but i dont want two interceptors, i want an interceptor and hptuners logging at the same time...
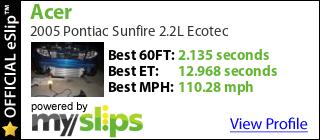
|Forged 8.9:1 Wiseco Pistons|Forged Eagle Rods|HPTuners|60trim|Tial Wastegate|
|Precision Intercooler|2.5" Exhaust|2.5" Charge Pipes|630CC Mototron Injectors|
|Stock: Fuel Pump, Transmission, Manifold, TB, Head, Head Gasket, Ignition, Suspension...|
Here's my thought. And I could be wrong but I'm mentioning it becauase I was wanting to do I think the same thing. I have a Scangauge II in my car to monitor different things, and it plugs directly into the data port under the dash. I was wanting to add a second data port behind the dash so that I could leave the Scangauge plugged in and have the cable up out of the way. That way the stock port could be accesible by a mechanic should I have to take my car in for service work. I'm selling my house and moving into an apartment so working on my own car is going to be a bit more difficult lol.
Anyway, my thought on this was that the data is fed by voltage, right? So what would it hurt by wiring in the second cable? All one would need to do is get the cable from a donor car (same make model and year to make sure wires match up) and splice it in. A good connection and fairly short wires should keep voltage differences to such a minimum that the two ports wouldn't interfere with each other.
The data is not a voltage, its a variable pulse width signal. The problem isn't splitting the ports, its addressing the right data to the right scan tool. Whatever you connect to that port has an address of 0x10, even if you split it in two....
Look at it this way... If you have two computers and you try to make them both use the same IP address, neither of them will work (well, in the computer world the first one who gets there wins), but its the same in principle. Both scan tools have the same "ip address" as each other, and the ECU is sending the same data to both of them. If the tool is getting a response that it didn't expect or ask for, then you can confuse it, or slow things down. This probably doesn't happen when you are using two of the same model and brand scanner, but start mixing and matching and you can have issues. The HPT cable puts the ECU in a special transmit mode so that a normal scan tool, like those gauges, WILL NOT UNDERSTAND WHAT THE ECU IS SAYING.
4cyltuner.com - Information Source For 4 Cylinder Tuners
Buy stuff from CarCustoms Ebay! Won't be disappointed!
Okay that makes sense. And HPT will make the signal unreadable by the Scangauge? That kinda sucks. I was hoping to keep it so I dind't have so many gauges and I wouldn't have to keep a laptop in the car all the time lol. Actually my plan was to install everything and bring the car to you to have it tuned, do it once and be done with it.
I don't know how well this would work, but could you use the outputs on hptuners into the analog inputs on the interceptor gauge? You'd have to set up how the signals are sent probably and you'd be limited to only 2 choices at a time for the gauge i think (until you change it with hptuners), but it might work. Shifted?
i don't know under which data bus type the cavalier computers work on...but on 1553 data busses if there is one or more devices that don't send/receive information when they are being tasked then the offending device is shut down by the bus controller. if two devices are attempting to send in formation at once or receive at once they then have to send a "finished" code after if there is more then one sent then the bus controller can terminate both devices. i know this is what is used on airplanes....if I am wrong tell me I don't know much about the data bus type on our cars I am just providing what I know about data buses from my field.
based on how shifted described it i think it works as like a login system where each device has to "log in" to the ecu and only one can be in there at a time because there is only one valid user name
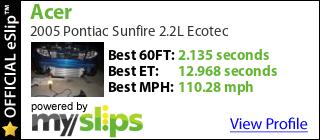
|Forged 8.9:1 Wiseco Pistons|Forged Eagle Rods|HPTuners|60trim|Tial Wastegate|
|Precision Intercooler|2.5" Exhaust|2.5" Charge Pipes|630CC Mototron Injectors|
|Stock: Fuel Pump, Transmission, Manifold, TB, Head, Head Gasket, Ignition, Suspension...|
Kinda...
Each device on the communication bus gets an address. The scan tool (whatever is connected to the OBD port), has an address of 0xF1 (this is hard coded into the scan tools as the expected response address). The ECU has an address of 0x6A. These are more like IP addresses than login's. So here is how the bus communicates:
The Scan tool sends the following bytes to request the RPM
0x68,0x6A,0xF1,0x0D,0x0C,CRC
The first three bytes are called the header:
Byte 1: Priority
Byte 2: Target Address
Byte 3: Source Address
Byte 4: Mode
Byte 5: PID
Byte 6: CRC for error checking
Sending this sequence of bytes to the vehicle, would get you a response like:
0x48,0xF1,0x6A,0x0D,0x4C,0x08,0x05,CRC
Byte 1: Priority
Byte 2: Target Address
Byte 3: Source Address
Byte 4: Mode
Byte 5: PID (This is the original PID + 0x40)
Byte 6: Most significant byte of value
Byte 7: Least significant byte of value
Byte 8: CRC
So, that response would mean the car is running at 2053 RPM.
As you can see, the scan tool ALWAYS tells the ECU to respond to address 0xF1. If two scan tools are on the OBD port, they are both listening to responses sent to 0xF1. If it gets a response that its not expecting, or in HPT's case, a response that it can't understand (since the mode that HPT puts the ECU in is a native language, much faster than OBD specifications and not standardized), one or both scan tools will stop working.
Its like having 2 computers on a network with the same IP...
4cyltuner.com - Information Source For 4 Cylinder Tuners
Buy stuff from CarCustoms Ebay! Won't be disappointed!
it sounds like a mil-std-1553 data bus. now does the programming of the ecu have an open address. because since the only one device can be tasked at any one time...that doesn't mean that you can only have one device at once. with this type of buss you can have an almost unlimited (talking for our app) amount of devices talking to this one buss controller( 60 some if I am correct).
what a krappy system to use....but oh well what do you expect bare minimum to get it functional and off the lot...
don't get me wrong I love my cav
Its not crappy, it just meets the needs. From a business standpoint it doesn't make any sense to add functionality into a system that you design that you'll never use. I create new industrial control products (like PLC's), and I won't add in features like "multiple programmers" because it just doesn't make sense to do it for our target audience. Why would you need the ECU and BCM to be in program mode at the same time? You can only send one file at a time, you can only guarentee packets with error checking to one host at a time (on a one wire system).
I'm sure on your MIL spec devices you aren't programming the flight computer, the data recorder, and the instrumentation all at the same time, you do it one at a time, same concept.
4cyltuner.com - Information Source For 4 Cylinder Tuners
Buy stuff from CarCustoms Ebay! Won't be disappointed!
that is why you have a bit at the end of the tranmission to make sure everything gets sent.....and yes all of these devices are on one bus all the ones you mentioned work on one wire. and the system I am talking about was brand new in the 1960's. but yeah you are right it is pointless to do monitoring and writing on the same time on our cars. it does not add to us. on the fly programming would be too expensive to get in to for our application...and the systems on one bus include....black box, servo cylinder actuation, air data, gps, inertial nnavegation system, terrain following, flight director, stall inhibition/ stability enhancement, plus a dozen others (enough examples).